MELT FLOW INDEXER (MFI) FREQUENTLY ASKED QUESTIONS
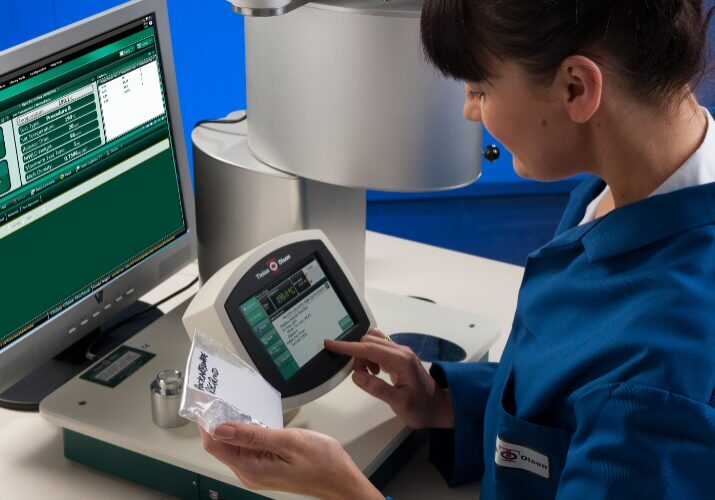
It heats and compresses thermo-softening resin, then measures resin extrusion rate through an orifice, under carefully controlled conditions;
- Precise and uniform control of resin temperature
- Accurately known applied weight
- Extrusion through a calibrated extrusion die orifice
- User-defined, totally reproducible automated methods
Rate of extrusion (typically g extruded / 10 minutes)
- Known as Mass Flow Rate (MFR)/ Melt Index (MI)/ Melt Flow Index (MFI)
Melt viscosity / flow resistance
• Measured at carefully controlled temperature and weight load
• High melt viscosity = High flow resistance
• Melt viscosity is inversely related to extrusion rate
• High extrusion rate = Low melt viscosity
Polymers consist of very long molecules, made by linking together hundreds, or thousands of small monomer molecules.
The basic structure of this long polymer molecule is known as the polymer chain.
Short, unbranched polymer chains slide past each other very easily leading to low melt viscosity.
More complex branched chains and greater chain lengths both make it more difficult for the chains to slide over each other, leading to higher melt viscosity.
For a particular polymer type, it is an indicator of mean molecular weight, (also known as relative formula mass)
High mass flow rate (MFR) → low flow resistance → low molecular weight
More broadly, it gives an indication of the expected physical properties of the finished component or product that is made from the resin.
So that the processor who uses that resin does not make any chocolate tea pots.
High MFR material may be easier to process, but important physical properties, such as performance over a range of temperatures, or impact resistance, are also related to molecular weight.
The performance of a finished product or component derives from key characteristics of the resin. Testing resin is the first link in the Quality Assurance chain. So........
• Resin suppliers must test their resin melt index
because.........
• Their customers will test the resin as a material acceptance specification.
Yes
Resin MFR is a key indicator of the end product quality.
It’s also a fast and inexpensive way to compare vendor resins, so resin users can reduce the risk of failures at very little cost to their operation.
It can, but sometimes it doesn’t
Melt Flow Rate (MFR) values can change because of;
• Handling and transport
• Storage conditions
• Improper drying
• Resin regrind
Yes
MFR testing can pinpoint;
• Poor incoming materials
• Inconsistencies between batches
• Improper storage at your own facility
• Inappropriate drying
• Any negative effects of regrinding material
• Other problems with your processing conditions
Yes
An injection molded polycarbonate component was found to crack when dropped. The virgin resin had an MFR of 28.5 g/10 min. Good resilient polycarbonate components were ground up and their MFR was measured, at 27 g/10 min, well within tolerance (+/- 30%).
A problematic, more brittle part had an MFR of 90 g/10 min. It was discovered that a defective batch contained a large amount of regrind, which had been thermally degraded in processing.
Yes
• ASTM D1238 ( Standard Test Method for Melt Flow Rates of Thermoplastics by Extrusion Plastometer)
• ISO 1133 (Determination of the Melt Mass-Flow Rate (MFR) and Melt Volume-Flow Rate (MVR) of Thermoplastics.)
• ...... and various other international standards
These standards require the measurement of mass flow rate (MFR) under standard conditions. Their manual and automated methods (A and B) are rather similar.
Standard and motorized configurations of the Melt Flow Tester (MP1200) both comply.
The MP1200 is a technology that we have refined by listening to our users, who are involved in;
• Resin supply
• Molding
• Extruding
• Compounding
• Recycling
A number of measures of resin performance can be made
• MFR (Melt Flow Rate), also known as the melt index
• MVR (Melt Volume Rate)
• FRR (Flow Rate Ratio)
• Apparent shear stress
• Shear rate
• Intrinsic viscosity
• Melt density
Yes.
The MP1200 can be upgraded with optional features, including ISO 1133 tools and an encoder-based programmable piston displacement transducer (or PPDT for short), for testing according to Procedures B & C (ASTM D1238) or for volume measurement tests (melt volume rate or MVR) and melt density calculations
The MP1200 features a modular design. If you start with the basic cut & weigh configuration for a Procedure A type test, the MP1200 can later be equipped with the following to achieve Procedure B and full automation;
• Optional automatic timing switch
• Programmable motorized weight lowering device (WLD)
• Encoder-based programmable piston displacement transducer (PPDT)
• Extrudate cut-off tools, (manual or motorized)
• Flow Rate Ratio (FRR) attachment
• Pneumatic purge & clean fixture
Yes
With Horizon, the user can;
Store - an unlimited number of test method settings
Recall - any previous test results at any time
Generate - test reports and SPC control charts
Control - multiple melt indexers from one PC
Analyze - data from more than one machine
Read - data from other physical testing equipment
• Flow Rate Ratio (FRR) attachment
• (requires optional automatic timing switch)
ASTM D1238 Procedure D requires that applied weight is varied during the test (up or down). This changes the flow rate at the extrusion and allows a flow rate ratio to be measured.
The weight change is triggered by the automatic timing switch.
The MWLD makes life easier and enables weight to be added at a user-defined interval when the resin is up to temperature.
Less user intervention and greater method reproducibility
The most common procedures are denoted Procedures A and B within ISO and ASTM specifications. They are similar in each standard. Procedures C and D are a little more complex but this machine can perform all of them.
Procedure A only needs the lower cost manual MP1200.
Manual cuts of the extrudate, at defined test temperatures and loads, are made at time intervals, which are indicated to the user by the software.
Cuts are weighed on an analytical balance. Masses are entered into the software, which then calculates the melt flow.
Procedure B is a volumetric measure of the extruded material. The PPDT option is required for measuring piston travel.
The extruded volume is calculated from the diameter (D) of the barrel and distance of piston travel during the test (L). Volume = π(D/2)2 x L (but note that the instrument does the calculation).
The melt volume rate (MVR) is calculated as cm3/10 min. From this value and the resin’s known melt density, the melt flow rate (MFR), in g/10 min can be calculated automatically. MFR = MVR x Density
The operator simply loads the barrel with resin and starts the test. The instrument calculates the results.
Procedure C is less common because it’s specifically designed to test high flow rate olefins. The test must be automatically timed and uses a special die, which has an orifice that is half the height and half the diameter of the more normal 2.1 mm orifice die.
Procedure D is referenced under ASTM D1238. It indicates how the MFR of a single sample changes under different loads, at the same temperature. It yields a Flow Rate Ratio (FRR) value for the material.
• Procedure D is a multi-weight test.
• Weight must be varied (up or down) without stopping the test
• Test must be completed at a constant temperature
• The Flow Rate Ratio (FRR) attachment is needed
For more information on the procedures, please watch the below videos.
Procedure B testing requires an accurate value for the resin melt density. A reference value can be used, but the test may be more reliable if you measure the melt density of the resin actually being tested.
The Melt Flow Indexer MP1200 can do both at the same time.
This is done by combining elements of Procedure A and B in a single test run, to obtain both the mass and the volume of the extruded material – hence, the density. The MP1200 fitted with the PPDT, using digital encoders, can be used to find both values.
References: https://www.tiniusolsen.com/list-of-products/mp-1200
Nexus Analytics is Tinius Olsen (a leading specialist manufacturer of materials testing machines) Sole Distributor in Singapore & Malaysia.
Book a free demo with us now!
Please fill up the form below. Our team will contact you as soon as possible. Thank you